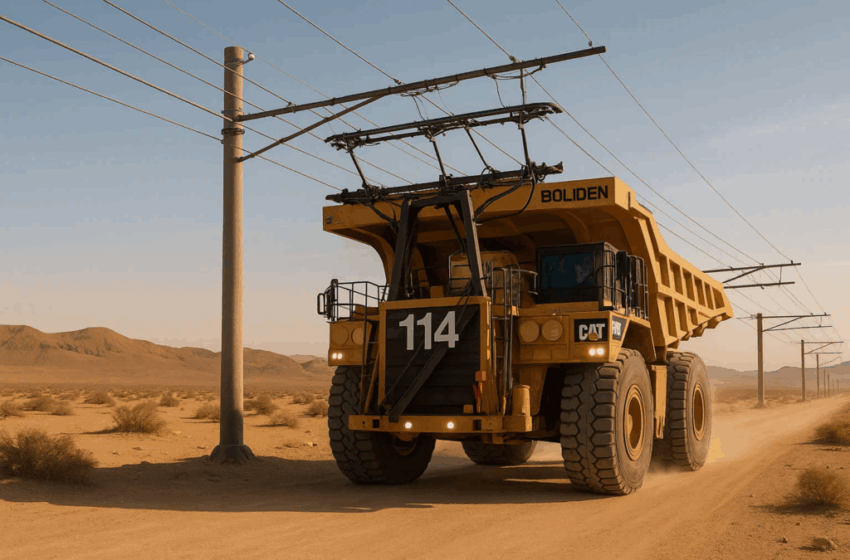
La mina eléctrica: Cómo la minería enfrenta el reto de las condiciones ambientales – Mch
Expertos coinciden en que las condiciones extremas donde se desarrolla la minería —como la altitud elevada, las temperaturas bajo cero o la alta humedad— tienen un impacto directo en la autonomía y el rendimiento de los vehículos eléctricos.
Por ejemplo, en ambientes de gran altitud geográfica se reduce la eficiencia térmica. El frío extremo limita el rendimiento de las baterías, y la baja humedad podría acelerar el desgaste de los sistemas electrónicos.
En ese sentido, Ignacio Muñoz, Product Marketing Manager de ABB en Chile, comenta que los equipos eléctricos “en altitudes elevadas o ambientes fríos requieren baterías con mayor densidad energética y sistemas de gestión térmica avanzados. De igual forma, diferentes químicas de baterías y perfiles de carga/descarga deben considerarse según el ciclo de trabajo y las rutas de transporte”.
En el caso de la infraestructura de carga, Muñoz cuenta que “también deben considerarse adaptaciones en los diseños que contemplen las condiciones climáticas y del sitio en que se realizan las operaciones mineras”.
A su vez, Pablo González, Product Support Director de Komatsu Holding South America, sostiene que “las condiciones operacionales pueden generar cierto impacto sobre el desempeño de los componentes eléctricos. El frío extremo limita el rendimiento de las baterías, y la baja humedad podría acelerar el desgaste de los sistemas electrónicos y los sistemas de gestión de carga”.
Ahora bien, González añade que “aunque estos desafíos no son despreciables, tampoco son inéditos para la industria minera. Requieren, sin embargo, el desarrollo y la validación de soluciones ad hoc que garanticen la confiabilidad de los equipos eléctricos en aplicaciones mineras de alta exigencia ambiental”.
Por otra parte, Joao Araujo, Business Line Manager de Load & Haul para la región en Sandvik, manifiesta que “el impacto en la autonomía de los equipos no se ve fuertemente afectado por las condiciones ambientales de las minas. Influyen mucho más directamente el perfil del trabajo, como las cargas, las pendientes y las distancias”.
Araujo agrega que “no obstante, para el perfil de degradación y envejecimiento a largo plazo de las baterías, sí es relevante considerar las condiciones climáticas”.
Monitoreo e Inteligencia Artificial
Actualmente, existe una amplia posibilidad de contar con telemetría avanzada en los equipos, baterías, cargadores y sistemas de enfriamiento.
En el caso de ABB, Ignacio Muñoz comenta que “es probable que las mismas plataformas de software actuales, con las que se planifica la operación minera y se administran las flotas de vehículos, incorporen en el futuro la integración de las variables de operación de la infraestructura eléctrica”.
Del mismo modo, el Product Marketing Manager de ABB en Chile afirma que “la analítica predictiva y la inteligencia artificial permiten tomar decisiones rápidas y coordinadas entre silos operativos. De igual forma, será posible monitorear en tiempo real el estado de carga, temperatura y rendimiento de cada vehículo, y usar herramientas que integran algoritmos de predicción, anticipando necesidades de carga o mantenimiento, considerando variables reales con las que se está trabajando”.
A su vez, Joao Araujo precisa que “en los equipos contamos con un sistema nativo de telemetría, que constantemente monitorea y comunica una gran cantidad de señales de rendimiento, comportamiento y estado de los componentes”.
Además, el representante de Sandvik asegura que “estamos constantemente estudiando formas de mejorar la recopilación, el análisis y la conversión de los datos en hallazgos accionables para nuestros clientes. Eso significa que la inteligencia artificial y la analítica predictiva, entre otras tecnologías, están siendo evaluadas continuamente para permitir su despliegue en los diversos productos que ofrecemos al mercado”.
Por su parte, Renzo Rosa, Account Manager Junior Minería de Liebherr, expone que “utilizamos la monitorización de datos en tiempo real, herramientas de visualización y diagnóstico remoto para supervisar y optimizar el rendimiento de la flota eléctrica, mejorando la disponibilidad, la eficiencia y la productividad de los activos, al anticipar mejor las necesidades de mantenimiento mediante IA y análisis predictivo”.
KPIs para evaluar la eficiencia energética y operacional
Desde el punto de vista operativo, Ignacio Muñoz destaca que “seguirán siendo clave los KPI tradicionales, tales como el consumo energético por tonelada transportada, la disponibilidad operativa de los equipos (OEE) y la adherencia al plan productivo (metas diarias)”.
El ejecutivo de ABB agrega que “tomarán cada vez más relevancia otras métricas, como los tiempos de carga versus el tiempo operativo, la eficiencia del sistema de gestión de tareas y energía, así como aquella que hoy impulsa la electrificación de la minería: la reducción de las emisiones de CO₂ en las operaciones, medidas por períodos de reporte (mes, trimestre, año)”.
Por su parte, Renzo Rosa indica que en Liebherr se consideran indicadores como el costo por tonelada, el costo total de propiedad (TCO) y el tiempo de funcionamiento operativo.
Desde la perspectiva de Sandvik, Joao Araujo sostiene que “los equipos eléctricos a batería son, por diseño, muy eficientes. Contamos con diseños de tercera generación, es decir, equipos que ya nacieron siendo eléctricos a batería. Al no ser reconvertidos, sus elementos y componentes ya permiten su máxima eficiencia, por sobre un 95 %. Para nosotros es más relevante monitorear la eficiencia operacional de los equipos, dado que la eficiencia energética ya está garantizada por diseño”.
En línea con lo anterior, el experto de Sandvik puntualiza que “es relevante monitorear la cantidad de ciclos por hora, la duración de los ciclos, la tasa de utilización de la capacidad útil, la autonomía de las baterías, el tiempo ineficiente debido al cambio de baterías (el cual puede verse afectado por interferencias operacionales), las velocidades medias, máximas y mínimas, la vida útil de los neumáticos y los elementos de desgaste, entre otros factores, que varían en importancia dependiendo de las condiciones y prioridades de cada operación minera, considerando sus propios desafíos y características”.
Desde Komatsu, se observa que “la industria está evolucionando favorablemente hacia la definición de estándares que incluyen los KPI de medición de desempeño de flotas electrificadas. Entre los indicadores más relevantes están: energía por tonelada (kWh/t), disponibilidad física (porcentaje del tiempo en que un equipo está disponible para operar), MTBF (horas) —tiempo medio entre fallas— y el tiempo de ciclo, un indicador clave para transparentar los beneficios operacionales de los sistemas electrificados”.
González concluye que “no se puede excluir de esta lista el TCO (costo total de operación) ni la huella de carbono (CO₂eq), ya que la comparación no será necesariamente lineal y deberá formar parte del análisis para evaluar el verdadero valor de estas soluciones de electrificación”.