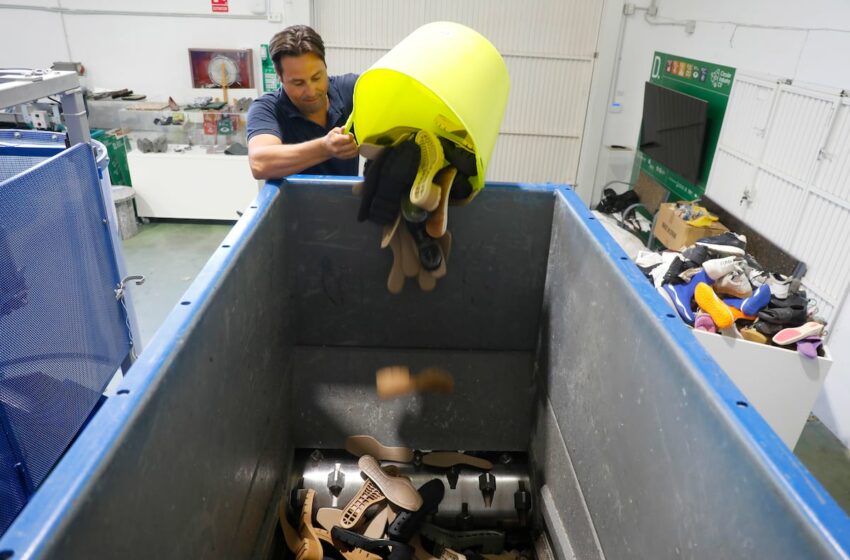
La difícil búsqueda de procesos para reciclar zapatos | Clima y Medio Ambiente | EL PAÍS
Una cubeta en forma de trapecio invertido, una cinta de transmisión, una trituradora y varios tubos para la canalización y separación de diferentes materiales. Esta planta a escala de laboratorio de pruebas, que cabe en una pequeña nave industrial, es la única que existe en España destinada a, de momento, la investigación del difícil proceso de reciclaje de zapatos. Se encuentra en la sede del centro de innovación y tecnología del calzado Inescop, en el municipio alicantino de Elda, uno de los puntos neurálgicos del sector en la provincia, junto a Elche.
“El calzado es un reto para químicos, ingenieros y biólogos”, afirma Borja Mateu, agente de Innovación del centro. “Si nos cuesta reciclar un envase de plástico, que apenas está formado por uno o dos componentes, es fácil imaginar lo complicado que es un zapato, que tiene de media una veintena, entre tejidos, metales, polímeros o adhesivos”, añade.
En España apenas se reutiliza un 5% del calzado utilizado. No existe ni “un contenedor específico para la recogida y separación” de este producto, lamenta Mateu. Y la legislación, con un real decreto para regular la economía circular del calzado en el horizonte de 2026, empieza a crear una situación de urgencia.
Los datos que maneja el instituto de investigación eldense, de 2023, reflejan que España es el vigésimo productor mundial de zapatos, con 80 millones de pares que salen de las fábricas. Además, la industria importa 315 millones de pares más y exporta 156. En cuanto a consumo, “salimos a 4,4 pares por cabeza al año y más del 95% termina en vertederos, incinerados y sin gestión”, asegura el científico alicantino. A un peso medio de 600 gramos por par, la suma se acerca a las 130.000 toneladas de potenciales residuos cada temporada. Y sin apenas salida en el creciente mercado de segunda mano.
“El zapato no entra igual que el textil” en el negocio de la reutilización, explica Mateu. “Se deforma con su primer uso para adaptarse al pie, incide en la salud del usuario si no se usa bien y es difícil de higienizar, ya que no se lava de la misma manera que la ropa”. Tampoco existen las plantas que lo separen, salvo un proyecto piloto en Tenerife. “En Europa, solo hay algunas que han empezado a funcionar en Francia, Países Bajos e Italia. Si aquí echas un zapato al contenedor, acaba en la basura”, sentencia.
La planta de Inescop se inauguró en 2022, aunque en realidad empezó a funcionar en 2019. “Usamos tecnología de otros sectores, como la minería o el procesamiento de plásticos, vidrio y cableado, para poder separar los componentes. El proceso ya lo tenemos, aunque aún se puede mejorar y lo estamos escalando”, indica Mateu, autor de una tesis doctoral sobre reciclaje del calzado para el departamento de Agroquímica y Medio Ambiente de la Universidad Miguel Hernández de Elche. El centro eldense mantiene acuerdos con ONG y entidades sociales, los únicos que recogen y separan hasta ahora los zapatos que se desechan. Una vez allí, la planta procesadora se enfrenta al problema de separar elementos “que ni siquiera se ven, como el cambrillón, que es una guía metálica que se inserta en la suela”. Pero una zapatilla, una bota o unos tacones pueden estar formados por “cuero, polímeros, cauchos, materiales sintéticos, fibras textiles, metales como el hierro, el aluminio o el zamak –una aleación de cinc, aluminio, magnesio y cobre- y adhesivos que, por definición, son complicados de separar”, detalla el especialista.
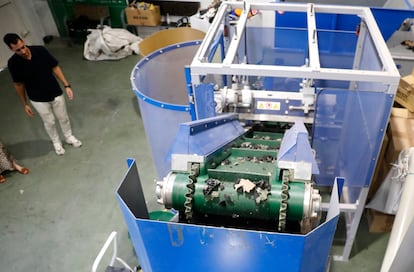
Las pruebas de Inescop consisten en triturar el calzado y separar, con diferentes procesos, los materiales férreos y las partículas resultantes en función de su tamaño. También dividen y reparten los materiales por densidad, con los textiles ligeros por un lado y los componentes de suela, cueros y espumas por otro. En sus laboratorios no se quedan ahí. “El reciclaje químico es el futuro porque permite que el material vuelva puro a la industria o a otros sectores, pero debe entrar limpio, sin impurezas, para poder efectuar la desreticulación de la goma EVA, la desvulcanización del caucho o la biodegradación y compostaje del cuero”.
Además, el centro alicantino está potenciando “el ecodiseño”. “Transmitimos a los fabricantes pautas para el uso de material reciclado y reciclable. De forma práctica, además, atendiendo a los procesos de producción, que lo entiendan como otro factor y no solo atiendan a precio, material de moda o color. Es el camino ideal. El único, en realidad”. Porque hasta unas aparentemente sencillas chanclas de caucho y PVC pueden suponer un reto para el reciclaje. “Si aplicamos los procesos para la desvulcanización del caucho, el PVC arde”, sostiene. Sin embargo, esta concienciación tampoco es sencilla. “La del calzado es una industria de industrias”, dice Mateu, “se basa en pequeñas fábricas que se especializan en determinados componentes y luego las grandes los unen y sacan a la venta”. “En esas pymes, que ya viven en situación inestable, es muy complicado hacerles ver la necesidad del reciclaje, pero nos estamos acercando”.
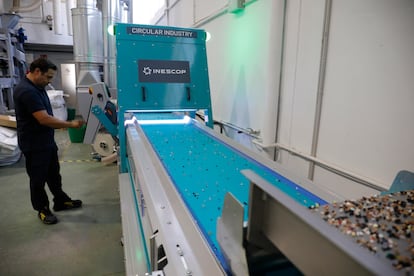
Con el impulso de la Unión Europea a la economía circular, todos los sectores están abocados a reciclar. Y ahí es donde entran los sistemas colectivos de responsabilidad ampliada del productor (SCRAP), que gestionan el reciclaje de residuos de las diferentes industrias. A principios de este mes de julio, el ministerio de Transición Ecológica sacó a exposición pública el real decreto que regulará los SCRAP del sector de la moda y el calzado, y que se prevé que entre en vigor con la llegada de 2026.
En España, de momento, hay dos, en estado casi larvario. Re-Viste, que cubre ambos campos. Y Gerescal, exclusivo del calzado, formado por nueve grandes empresas de toda España y cuyo director ejecutivo es Rafa Reolid, que insiste en que “el calzado no se puede meter en el mismo saco que el textil”. “Nuestra función es dar soluciones a los fabricantes y distribuidores para reciclar zapatos”, avanza.
Ya han establecido “acuerdos con ONG como Caritas o Humana y con puntos limpios de diferentes consorcios de residuos”, para la recogida selectiva. Reolid admite que aún se trata de “declaraciones de intenciones que se afianzarán cuando salga la normativa reguladora”. “Las ONG suelen tener tiendas de segunda mano, pero lo que no venden lo suelen mandar a países de África, Oriente Medio o el sureste asiático”, señala. “Ahora, nosotros se los compraremos y los llevaremos a reciclar”. El destino de los zapatos usados será “en primer lugar, la segunda mano”. “Luego, la regeneración energética, es decir, destinarlo a la alimentación de calderas en industrias como las cementeras, por ejemplo”. “El tercer camino sería la pirolización”, es decir, la descomposición del calzado en diferentes materiales, “como la suela o los aceites, que se pueden usar en la industria petroquímica”. Y, por último, en la parte más pequeña, se espera que vaya destinado al proceso de reciclaje que está probando Inescop “con una máquina que habría que industrializar”. De momento, no se puede llegar a una mayor proporción de reciclaje con los conocimientos actuales.
Aunque lo ideal sería utilizar estos residuos de zapatos en la fabricación de otros zapatos, y existen proyectos para reutilizar el material de la suela en la fabricación de otras suelas, esto también es muy complejo hoy en día. “El residuo del zapato no tiene por qué volver al calzado”, avisa Reolid, “es más fácil que vaya hacia el mueble, por ejemplo”.
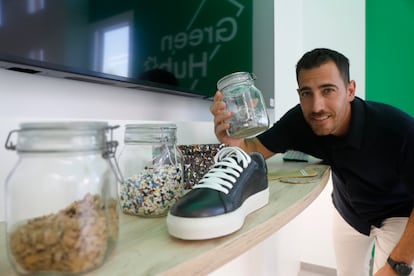
Ya hay firmas que los reviven como material decorativo y expositivo en sus tiendas, dicen en Inescop, donde las piezas trituradas también se aplican en la elaboración de bancos urbanos, suelos para parques infantiles y rocódromos e incluso “asfalto para el tráfico rodado”.