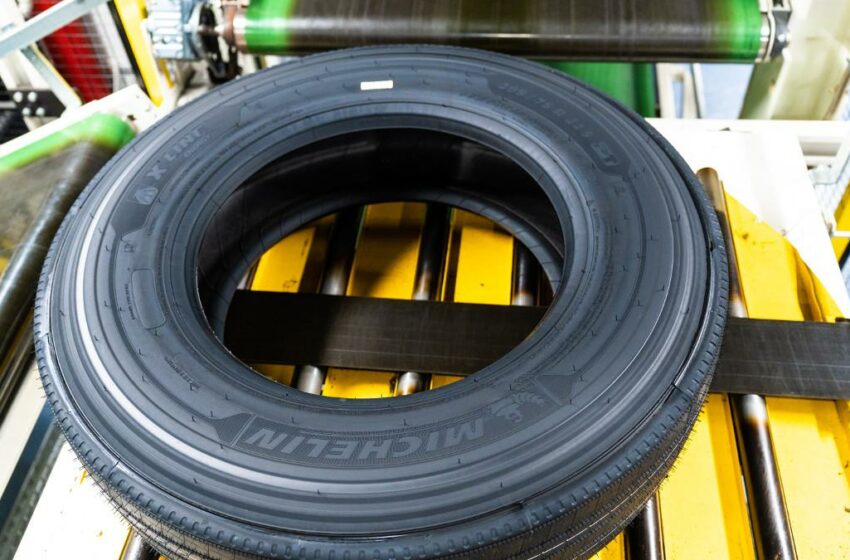
Descubrimos el secreto de los neumáticos Michelin
Elegir un neumático no es tarea fácil para el comprador. Es uno de esos productos en los que no se percibe una diferencia fácilmente reconocible y en los que el precio, o la oferta del día, suele ser el criterio más utilizado. Detrás de un neumático existe un proceso de fabricación muy complejo y tecnológico, y Michelin eligió la mejor manera que existe para podernos argumentar el porqué de su liderazgo tanto en ventas como en calidad, llevándonos a la factoría que posee en Aranda del Duero, especializada en la fabricación de neumáticos de vehículos de gran tamaño, concretamente de camión, autobús, autocar y metro.
Aunque Michelin es en origen una empresa francesa, casi se puede considerar más española que muchas otras que presumen de serlo, pero que producen sus productos en países asiáticos. Lleva instalada en España desde 1932, y en la actualidad dispone de cuatro plantas de fabricación que convierten a España en el segundo centro de producción del mundo en toneladas y el más importante del Grupo en Europa, por delante de Francia.
Michelin como compañía demuestra un alto compromiso con la sostenibilidad con un objetivo claro: el 40% de los materiales de sus neumáticos debe ser sostenible para el ejercicio 2030, mientras que para 2050 el 100% de los materiales utilizados será reciclado, reutilizado o sostenible.

Michelin demuestra un alto compromiso con la movilidad sostenible
Y ya si nos centramos en la fábrica de Aranda del Duero, rápidamente pudimos percibir la estrecha relación entre Michelin y la propia Aranda forjada a lo largo de los más de 50 años de historia de la planta. Realmente tienen que estar orgullosos puesto que Aranda es la mayor fábrica de neumáticos de camión del Grupo Michelin, con una capacidad de producción anual de 15.7000 toneladas. Supera los 1.200 empleados, y es un referente en el grupo, en cuanto a excelencia operacional e investigación y desarrollo, estando siempre inmersa en una continua transformación y evolución. Un dato a tener en cuenta es que dos tercios de su producción se queda en Europa, yendo el resto sobre todo al mercado norteamericano.
El que una marca te enseñe las entrañas de una planta de producción, en este caso de un tipo de neumático tan exigente y abocado a una utilización tan intensiva, como es el de camión, te hace comprender el porqué de muchas cosas, como por ejemplo que las carcasas de camión Michelin sean las más codiciadas por las empresas dedicadas a recauchutar neumáticos de camión.
Nos mostraron todo el proceso de fabricación desde el principio hasta el producto terminado final, pudiendo comprobar de primera mano la importante automatización de los flujos de producción. Pero sobre todo la relevancia que le dan al control de la calidad de todo el proceso, arrancando desde la producción de las propias materias primas. Sirva de ejemplo la indicación que nos dieron de no tocar bajo ningún concepto las varillas metálicas con las que fabrican los aros que integran los neumáticos, puesto que cualquier mínimo resto de grasa puede impedir una correcta fijación de los materiales y producir un neumático que dé problemas de cara al futuro.
No voy a describir todo el proceso productivo de las carcasas de los neumáticos, porque no es cuestión de aburrir al personal, pero allí donde otras marcas terminan Michelin sigue afinando e incluyendo capas de materiales. Sí, en efecto, por fuera todos los neumáticos son iguales, pero es importante conocer todo lo que hay detrás. Por ello, Michelin no duda en garantizar que sus neumáticos mantienen todas sus cualidades hasta el final de su vida útil.
Son capaces hasta de producir neumáticos “vivos”, que al ir desgastándose el dibujo aparece una nueva estructura que sustituye a la anterior, ya desgastada, prolongando con ello la vida del neumático. Todo ello producto de un proceso muy complejo a la hora de la cocción final.
Por otra parte, y en relación con los neumáticos de camión, la marca cuenta con Michelin Connected Mobility, una solución integral que permite a las flotas de camiones operar de forma más segura, eficiente y sostenible mediante la conexión de los neumáticos con la incorporación de un chip en cada uno de ellos. Gracias a una combinación de soluciones relativas a la gestión de neumáticos, tecnologías y algoritmos propios para recopilar información, este sistema ayuda a las empresas que lo integran a ahorrar costes, siendo mucho más sostenibles y eficientes. Lo interesante es que se adaptan a las necesidades de cada compañía, ya que no todas persiguen los mismos objetivos. Unas buscan mayor eficiencia en le consumo, otras llegar antes a destino, o transportar la mayor cantidad de carga posible.
La factoría de Aranda produce todas las gamas Michelin en el mundo del camión. También fabrican los neumáticos de Metro con los que equipan instalaciones como el tren T4 aeropuerto Madrid, Metro de Paris, el de Santiago de Chile, México DF… Son muy curiosos puesto que pueden parecer muy similares al neumático de camión, pero la zona de contacto es completamente diferente. No llegan a ser “slicks”, pero casi.

Visitamos la fábrica de Michelin en Aranda del Duero
En resumidas cuentas, la marca Michelin lo que sí aporta es la seguridad de que detrás de cada neumático existe una inversión muy importante, tanto económica como humana, en investigación y desarrollo, con el claro objetivo de seguir progresando tanto en sostenibilidad, seguridad y duración de los neumáticos, todo ello trasladado a un proceso productivo muy exigente con el fin de lograr la excelencia en el producto. Al final pueden resultar un poco más caros, pero realmente estás pagando un producto líder en todos sentidos. ¿Vale la pena la inversión? Personalmente pienso que sí. Y más si tenemos en cuenta que el neumático es la única pieza de nuestro vehículo en contacto con la carretera.